hi everyone! i hope you all had a lovely weekend! my husband is out of town this week so that means that i will be clattering away at the sewing machine during my evenings, trying to make decent headway on my spring wardrobe. it also means that i'll be nerding out with harry potter audio books - which i practically have memorized - all week long!!!
change of subject! you guys seemed pretty intrigued by
my plans for the "draped leather jacket" so i thought i would share some of the behind-the-scenes action. i'd like to share some of my "design process" for this jacket, since i drafted the pattern myself, and also some of my experiences in working with the lambskin (i think in my last post i called it sheepskin, but its actually lambskin).
first - a disclaimer: you guys. i am not a designer. i have zero background in this stuff. i've never even taken a class. i have one pattern making book that i've had for less than three months and i'm the queen of google searches. thats the extent of my knowledge. so please don't think of any of this as some sort of tutorial, or of me as some voice of authority. i don't know what i'm doing! this is just more of a chronicle of my experimentation, and, despite the fact that i don't know the right way to do a lot of this stuff, i'm happy with the results - for me! the same is true of working with leather. this was my first time handling the stuff so it was all a learning experience...
now that i got that off my chest, lets talk about my fumbling experience with pattern drafting...
i started with my sloper. this was the finished state of it after many hair wrenching re-drafts. actually i think the sleeves on this guy are still sucky, but i gave up. also, please ignore the fact that all these muslins are a wrinkled mess - they've been living in a ball on the edge of my sewing table. aaaand please ignore the ripped "v" at the neck. in a state of fitting frustration i tore open the muslin - incredible hulk style - only to realize that it solved the majority of my fitting woes... sometimes channeling a bit of roid rage has its benefits...
using my sloper i was able to make a torso block (which is basically the same thing as the bodice in the first picture, except that it extends down to hip level) and from that i drafted a basic two-dart jacket. i added ease and extended the shoulders. this first try was really big all around so i pinched out excess fabric at the front and back darts and the side.
the next go-around was a bit more flattering, but i still had some excess in the front (you can see how i pinned it out). i also experimented with the construction on this one, sewing the sleeves in flat and then sewing up the side seam and underarm seam in one go. this worked really well for me.
this next version was sewn up in some creepy polyester stuff thats been hanging around for way too long. (side rant - why can't i get polyester to press flat? also, why does it smell like a 70's basement when i press it? that stuff is just icky...) here i converted all my darts to princess seams - which i had to take in because apparently i'm not as busty as i thought. i was pretty happy with this muslin and considered using it as my final draft.... except for the sleeves!!!
a word about sleeves... again (deeeep siiighhhh) so for this jacket i was very worried about the sleeve ease because i knew i was going to be sewing it out of leather and, well, leather doesn't ease. so i drafted a sleeve and armhole that had zero ease.
you guys. i'm sure a lot of you have read the article on fashion incubator about sleeve ease being unnecessary and its all about the shape of the sleeve cap/armhole? if not, you can read it
here. but i caution you. after i read it i felt like i had entered myself into the extreme sports of sewing. all of a sudden it was like
"sallie just parachuted into an active volcano - but can she draft a sleeve without ease?!?" i think it caused more problems for me than if i had just worked with the stupid looking sleeve draft that was in my book.
here's the thing - again, from my limited experience. to make a sleeve that had zero ease i had to extend the shoulder seam about 1/2 inch. and it worked. and it looked...
okay. but i just felt that, design wise, the wide shoulder wasn't the most flattering. as you can imagine, it made my shoulders look wide. so i decided to shorten the shoulder seam again and add sleeve cap height to compensate for the roundness of the upper shoulder. i figured my leather would be able to handle some gathering, as long as it wasn't excessive. and... it worked! so while i think that perhaps sleeve cap ease
can be eliminated it will alter the design of your look. i just can't figure out how you'd make a sleeve with zero ease work without having a wider shoulder.
reading this post helped me disqualify myself from the extreme sports of sewing and just freaking make it work!!
so, the conclusion of my sleeve saga: don't get caught up in chasing the mythological sleeve. its not worth it and you'll end up trying to prove something to yourself, which is, in the end, pointless. just make a sleeve that works and move on with your damn life! my final sleeve? meh. i'm not in love, but it looks okay to me.
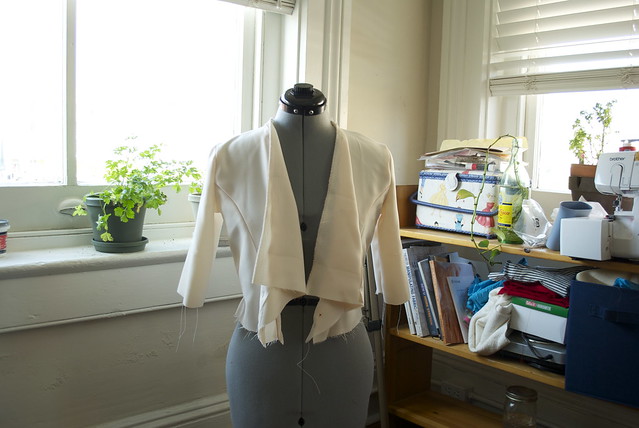
for this muslin i worked with the sleeve ease and shorter shoulder seam and found that it resulted in a very comfy sleeve (armhole looks weird here because i pressed it weird - promise). i almost started going down the rabbit-hole of fitting (over-fitting?) only to stop myself. i decided i liked the look of this jacket. it may not be the most "correct" fit in the world, but it fit the way i wanted it to and so i decided to focus my attention on drafting the draped front that i wanted. this was really the fun part. to do this i just cut a few triangles and pinned them together until i got the sort of shape that i had in mind. its certainly not an earth-shattering design, but it was fun to figure out.
a whole mess of discarded patterns and one dorky kitty
at this point i made all the final changes to my paper patterns and wrote out some instructions for myself to i could walk myself through the construction in my head.
then i cut out the leather.....
yes that is a brick up there on the right. it is my most favorite of pattern weights...
as i mentioned, this was my first time working with leather. i blame it all on amy from cloth habit for casually mentioning that she was going to be making this fabulous coat with leather trim. before this - i had never even dreamed of sewing with leather. but because of her the idea impregnated itself in my brain, and - after the usual gestation period - i now have a leather jacket baby!
here's some of my thoughts on working with leather - in no particular order:
- this stuff is awesome!
- really, a dream to work with!!
- imagonna make everything out of leeaaathhhherrrrrrrr!!!!!
so yeah. i liked it.
i traced my pattern pieces onto the leather hides (it took 4 hides to make my jacket) i followed this advice, once again from fashion incubator, on how to lay out your pattern pieces. then i just cut the pieces with my rotary cutter. no weird shifting, no fraying... easy peasy lemon squeezy.
i did a few tests with some scraps, figuring out needles and stitch length and top stitching. since the leather i was working with was pretty thin and drapey my regular universal needles worked okay, but the leather needle made a cleaner hole and i think it handled thicker layers better.
i had read in a bunch of places on ye olde worlde wide webb that a teflon foot was recommended for sewing leather. i didn't have one and didn't feel like buying one so i used my even feed walking foot. worked like a charm.
the same world wide web told me that pinning leather was not advisable since it will leave permanent holes in the leather. a few sites suggested to clip the leather pieces together with bulldog (binder) clips instead. i tried this but found that the clip would get caught on the edge of my throat plate on my sewing machine and yank the leather as it was being fed through. so instead i decided to just use plain old masking tape and taped my seams together. also (shhh) i used pins. yeah. i did. freaking rebel over here. i just made sure to pin in the seam allowance.
pressing seams was another switch up from your standard fabric sewing. i didn't even try to iron the leather, i just assumed it wouldn't work. so i bought this little ink roller (brayer) and rolled it over the seams to flatten them a few times, then used a thin layer of rubber cement to tack my seam allowances down. fun!
some other firsts for me on this project - working with rayon bemberg (ambience stuff) and bagging a jacket lining (had to modify this a bit since i left the front edge of the jacket unfinished because leather doesn't fray!!!).
really, the whole thing came together quite quickly and without any drama. maybe its because i essentially sewed the jacket 3 times before i set to work with the leather, or maybe it was just an easy pattern. but whatever. i finished the jacket last night (at the same time i finished listening to deathly hallows for the 455th time... me and harry potter, we're so in sync!) and i really like it!
i'll post pictures this week - scouts honor!
xx